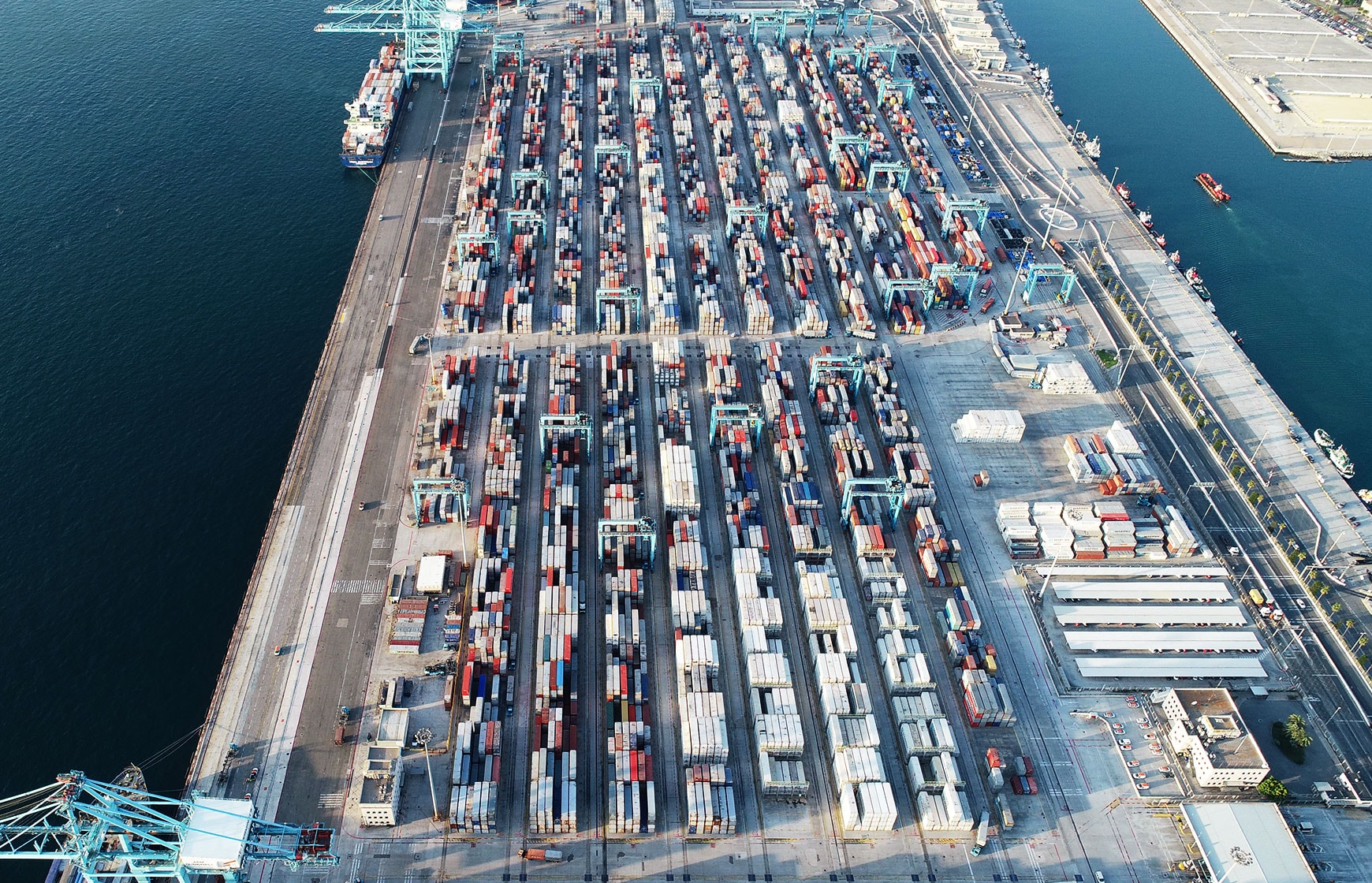
Lifting the Standard of Efficiency
Our Lean based Business System, known as the APM Terminals' Way of Working, is the backbone of our ambition to be the World´s Best Terminal Company. We strive for every process and every action to be directly translated into value for our customers - with no waste.
Our Way of Working was introduced to APM Terminals in 2018. Ever since, thousands of our frontline and office employees have been trained in the Lean methodologies and are successfully using these tools and skills to identify process waste and drive continuous improvement. Our Lean tools and methodologies that form the foundation of our Way of Working are used across all terminals, creating standardisation and one way of improving.
We are continually looking to lift our standards of efficiency and reliability and to create more value for our customers with zero waste. Our Lean methods make waste buckets in our processes visible and our highly trained and motivated people work to resolve these. I refer to this as 'all brains and hearts in the game'.
It all starts with waste
The basis of Lean operations is a relentless identification and reduction of waste. Waste refers to everything we can identify in the process that does not add value for you, our customers. At APM Terminals we have identified eight types of waste: Transportation, Inventory, Motion, Waiting, Over processing, Over production, Defects and Skills. We continually strive to reduce waste and improve our processes, so we can serve our customers better every day.
Improvements in these areas are driven by Kaizen (continuous improvement) Events. These are the beating heart of Lean. Opportunities for improvement are endless. Even if we think we are already doing well, we encourage our employees to look for better ways of doing things and seek perfection. And although we know perfection will be unattainable, by chasing perfection, we will reach excellence.
Way of Working House
Our Way of Working house shows our strong commitment to our customers. We start with a solid foundation of standards and stability. The roof of our house is our deep customer focus.
By truly understanding what our customer´s needs are, we drive the right improvements to be able to serve with the highest safety, the best quality, the best delivery at the lowest cost. Our goal is for every customer to experience the high level of performance and reliability in all our terminals globally.
Lean principles we've adopted...
How is our Way of Working lifting standards?
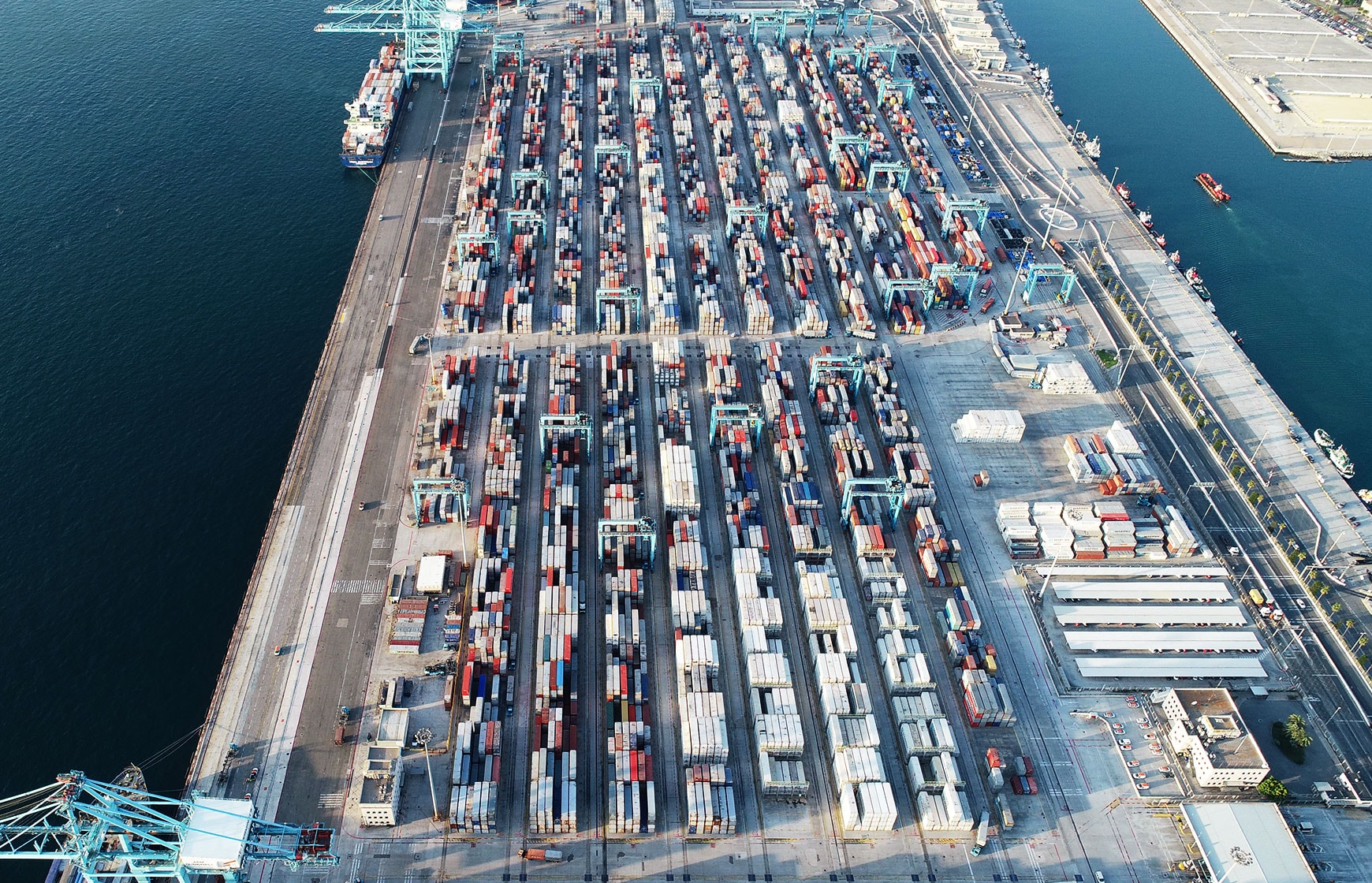
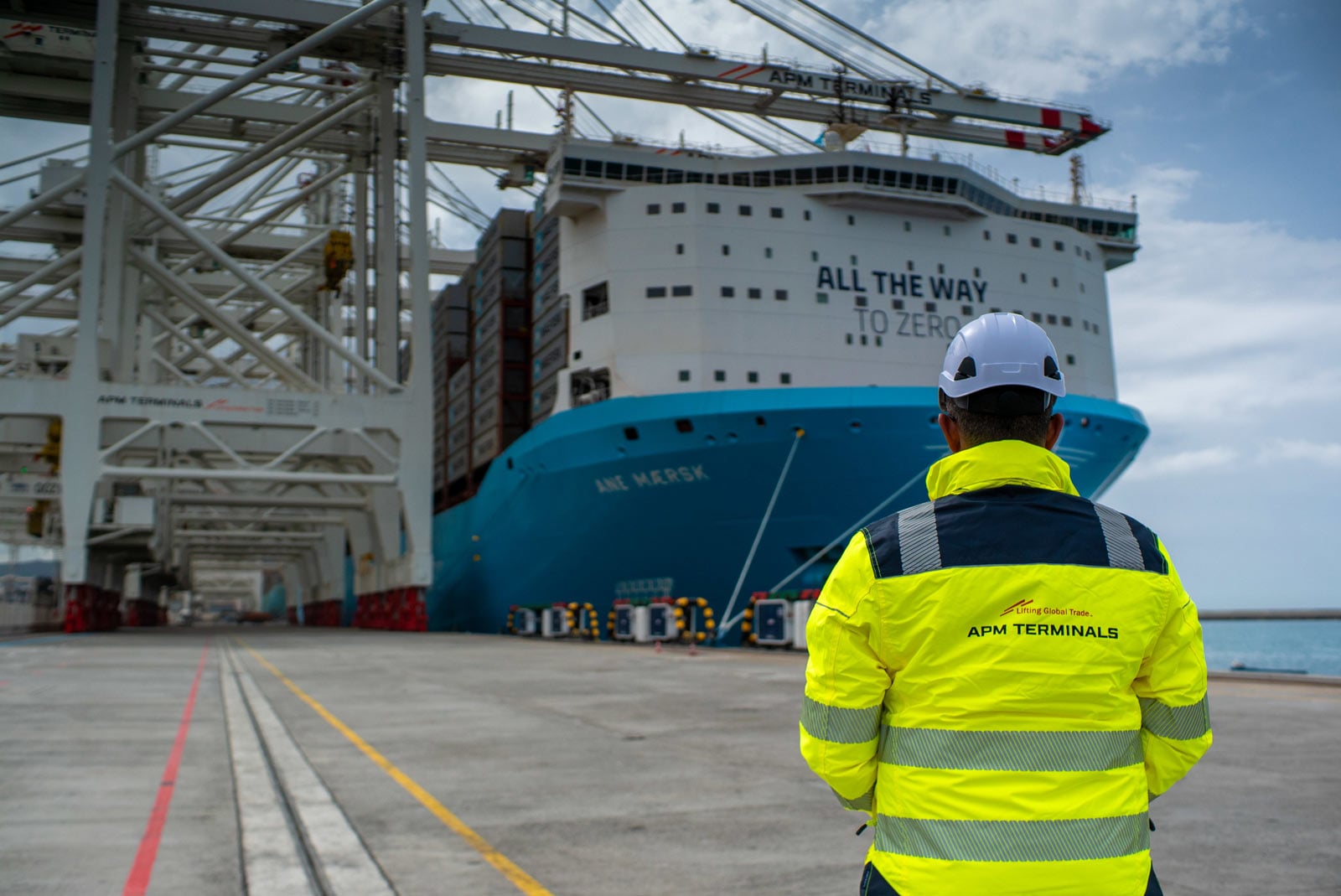
APM Terminals hubs to help Gemini Cooperation achieve 90%+ schedule reliability
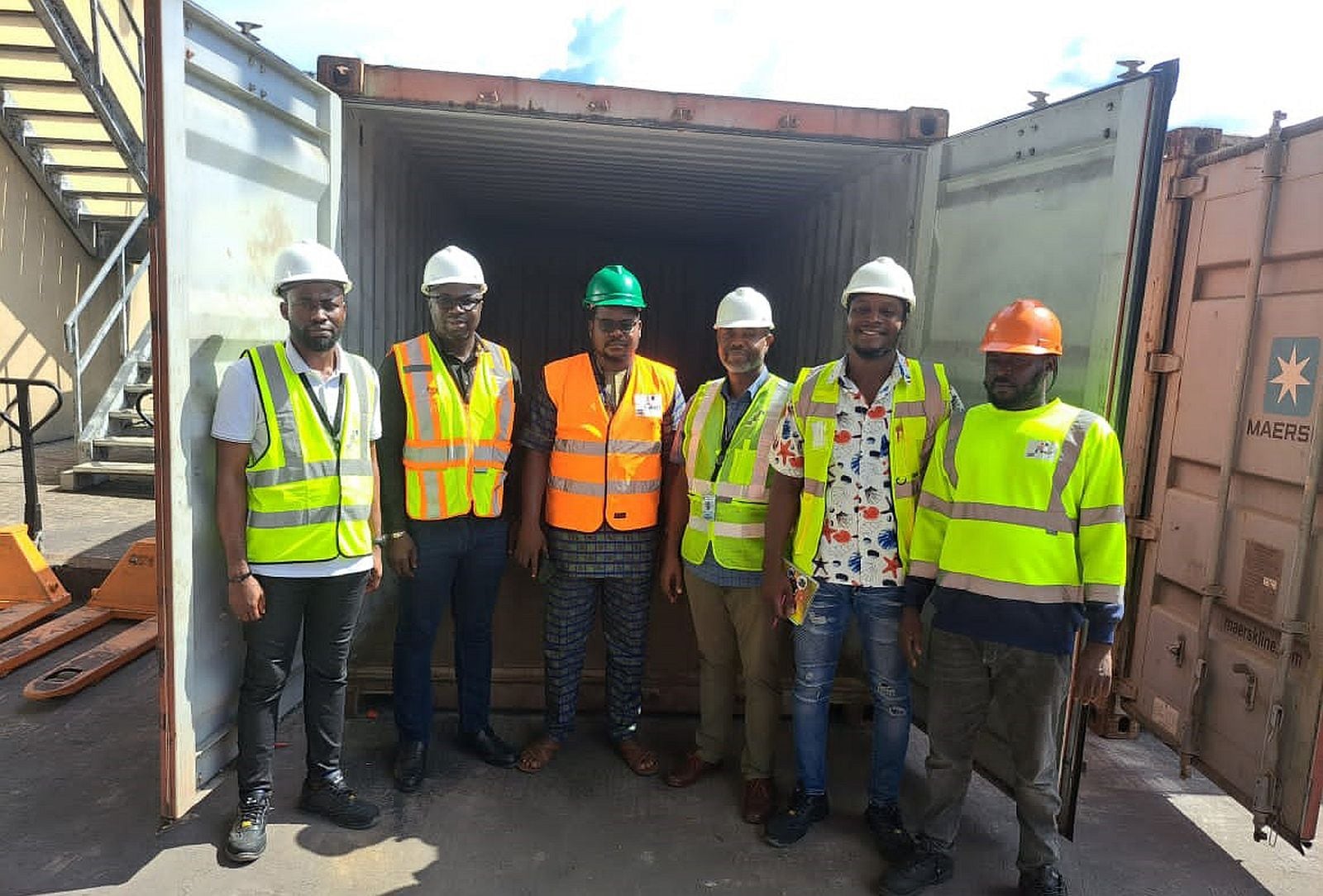
West Africa Container Terminal applies Lean methodologies to improve CFS efficiency
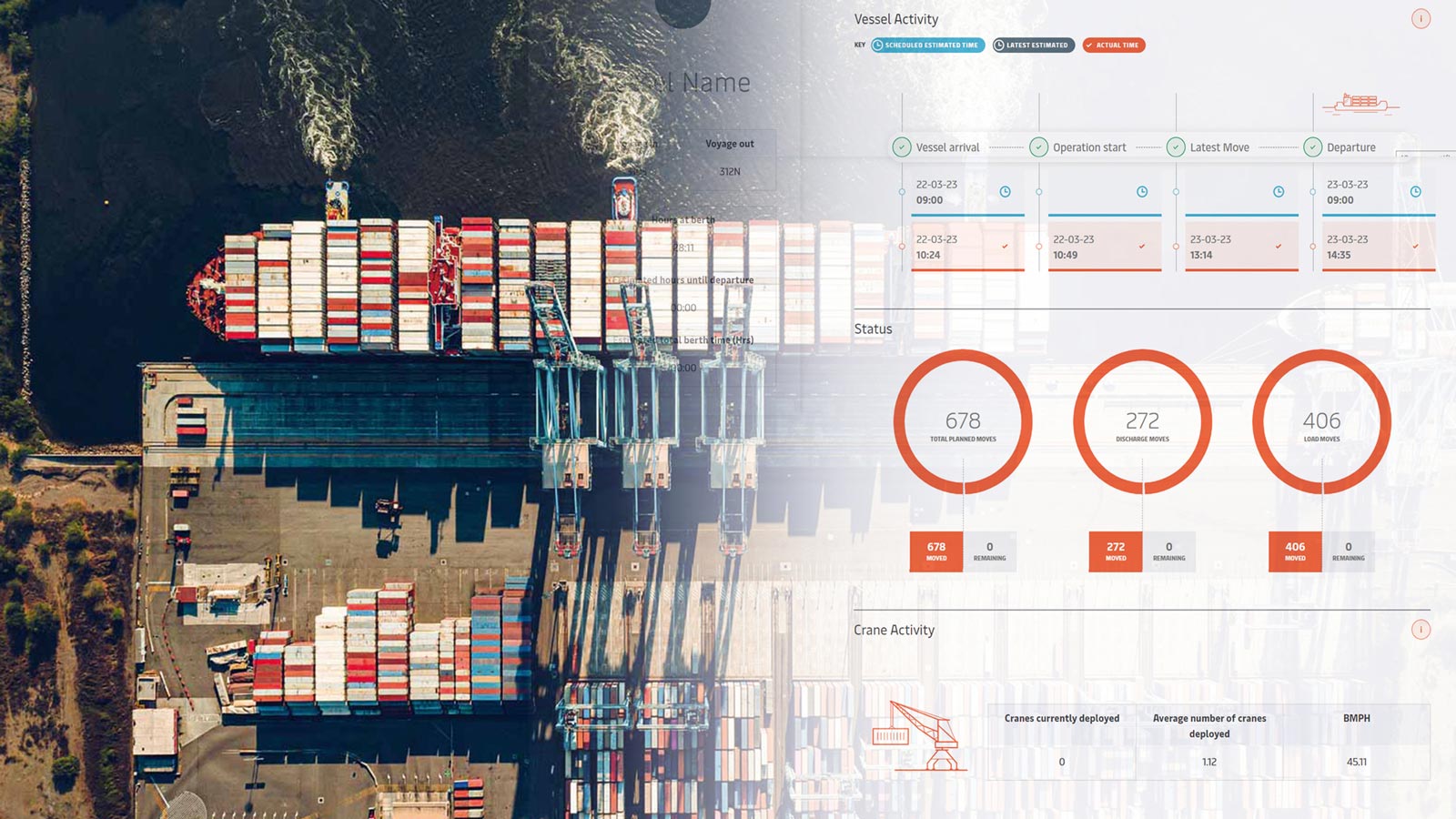
New Shipping Line Dashboard supports port stay reduction at APM Terminals
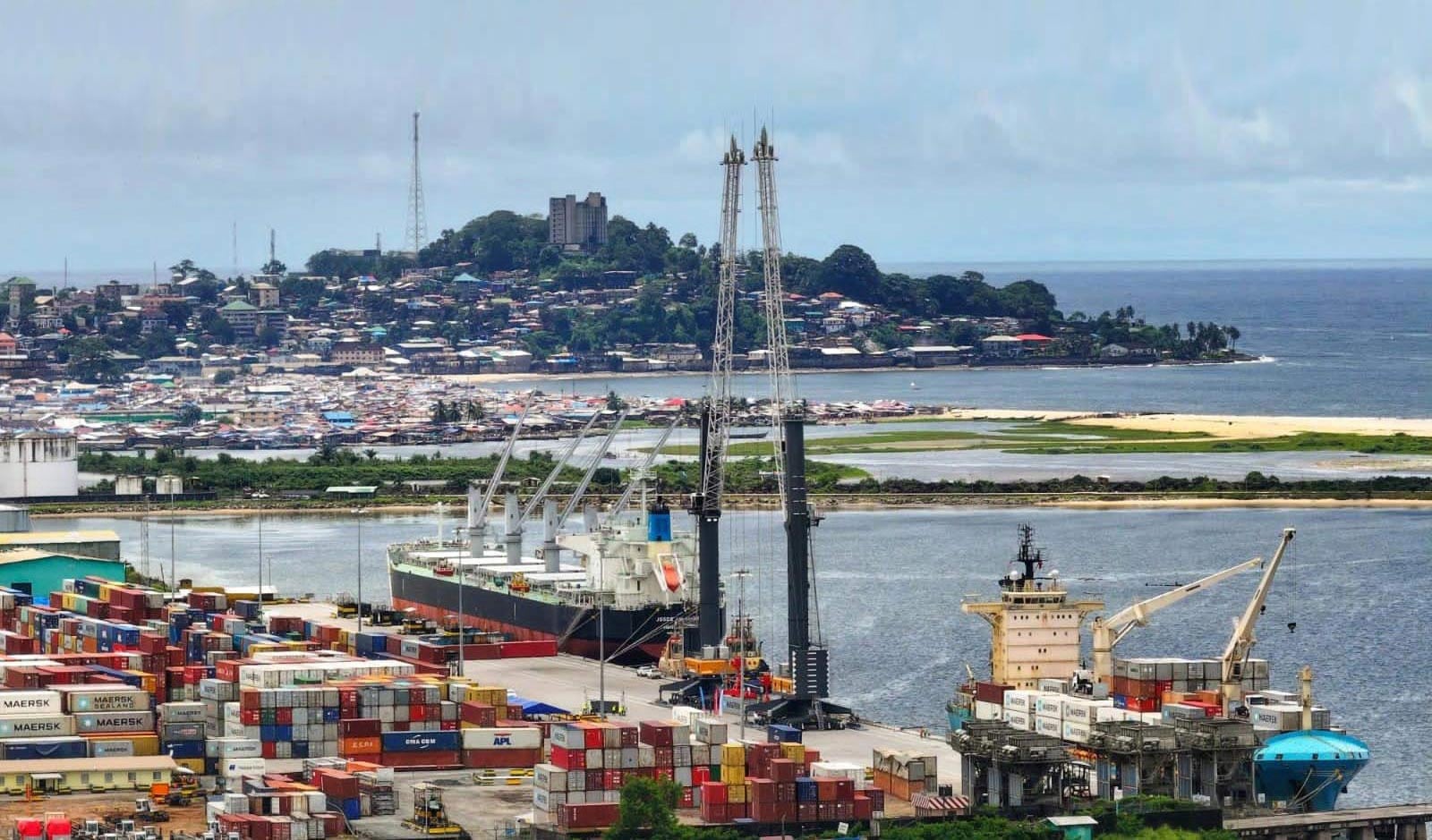
New cranes and deeper draft boost efficiency at APM Terminals Liberia

Record reduction in port stay and gate turn times at APM Terminals Moín
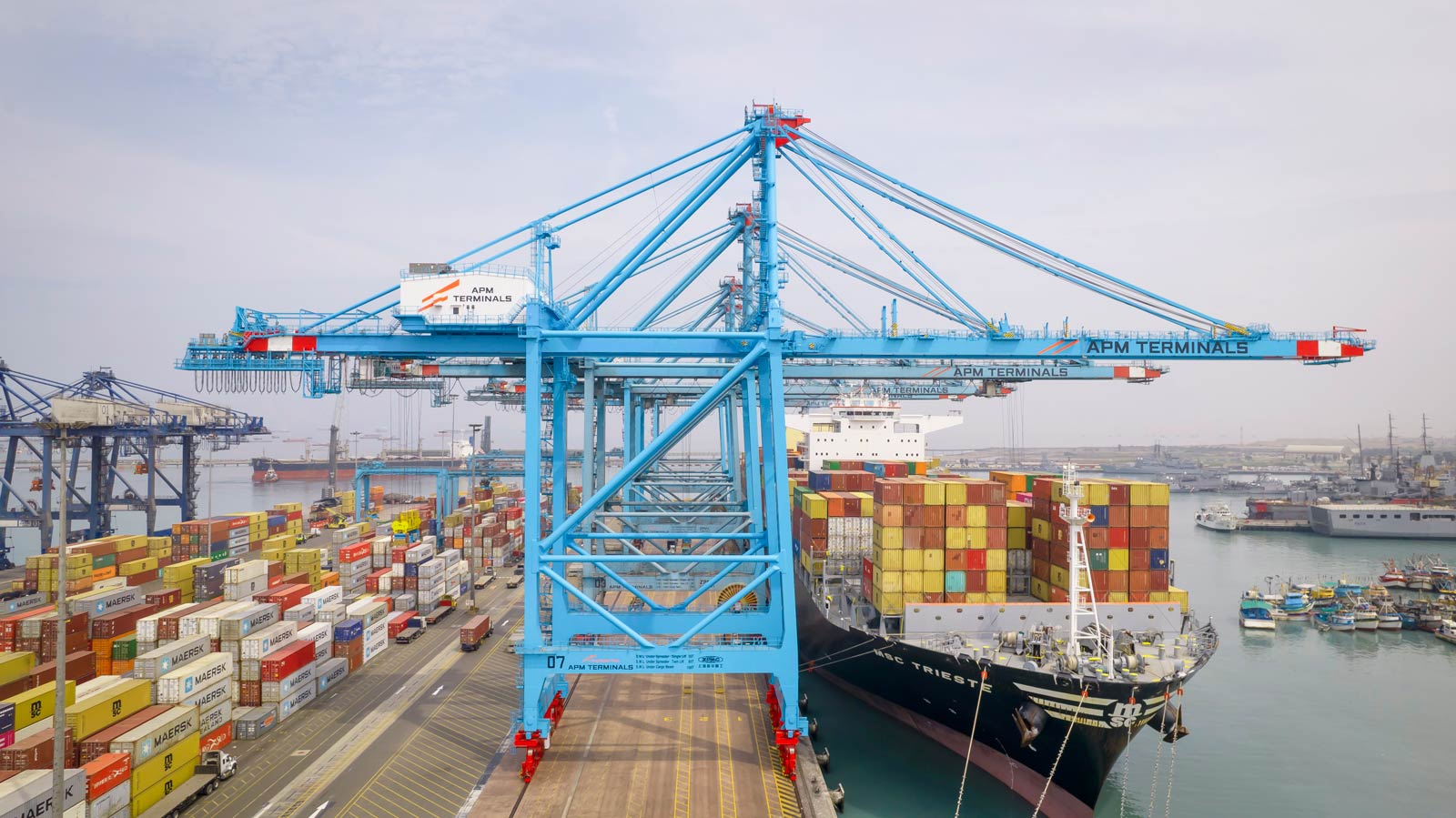
APM Terminals Callao exceeds one million TEUs for the first time
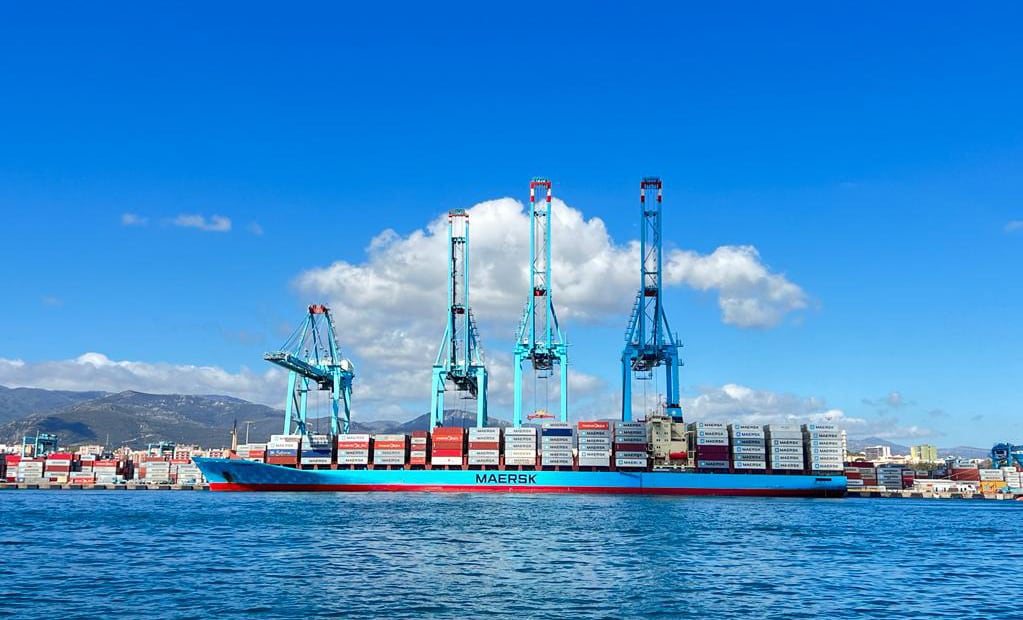
Record TEUs lift on Luna Maersk at APM Terminals Algeciras
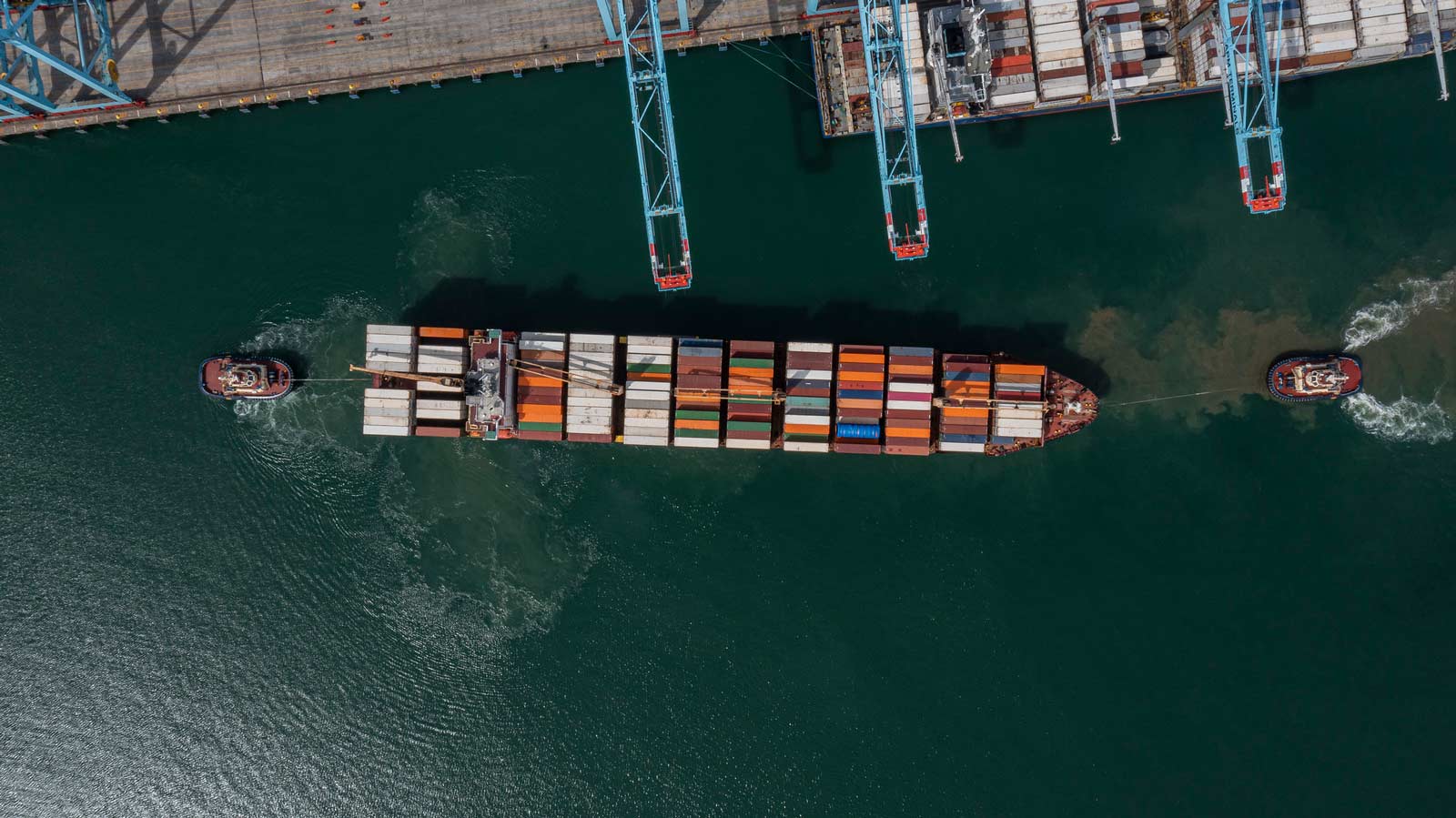
Blog: Embracing the unpredictable – by CEO, Keith Svendsen
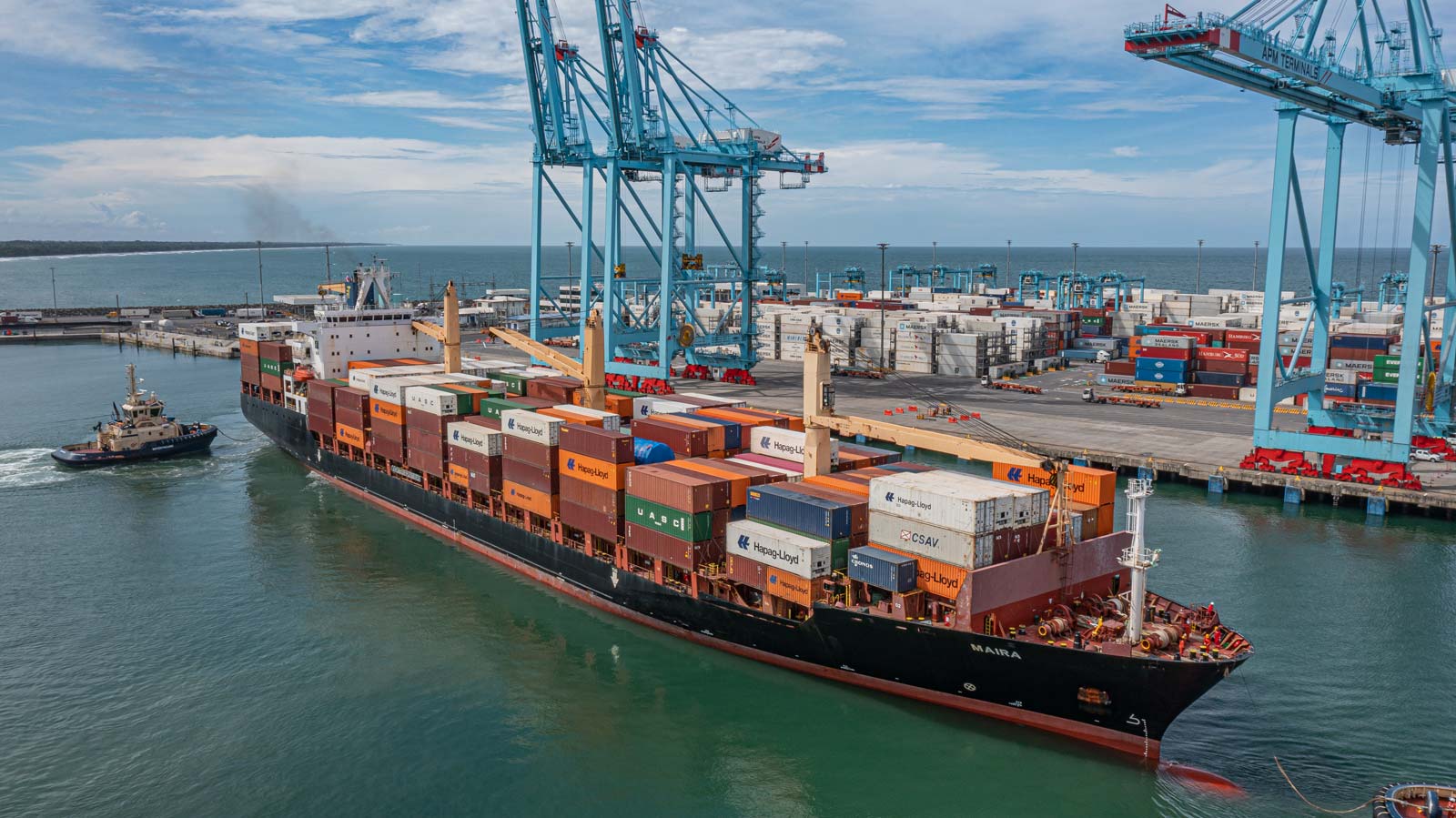
APM Terminals Moín reduces vessel idle time by 50% in just ONE year
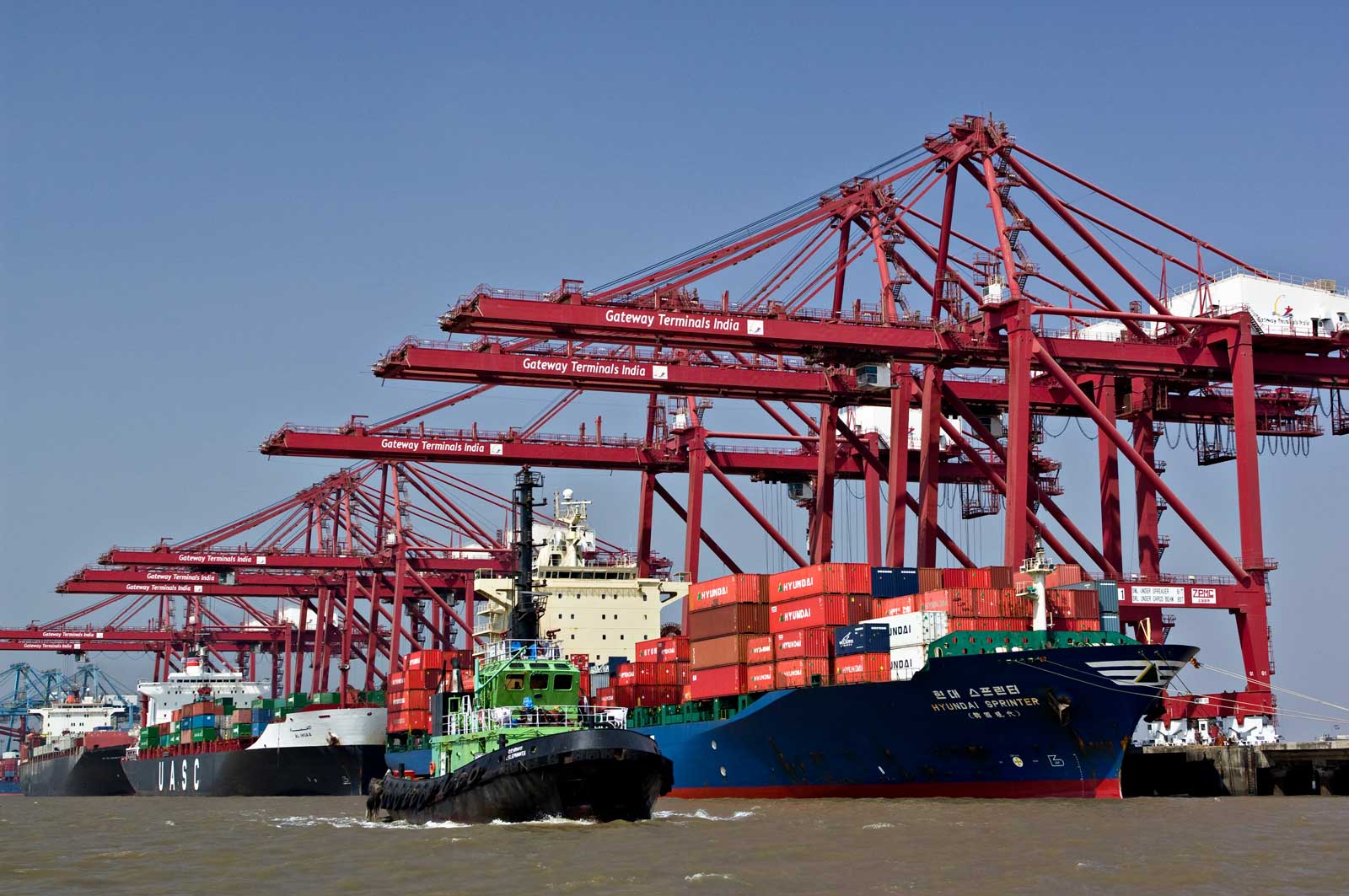
APM Terminals Mumbai leads Indian Performance Index
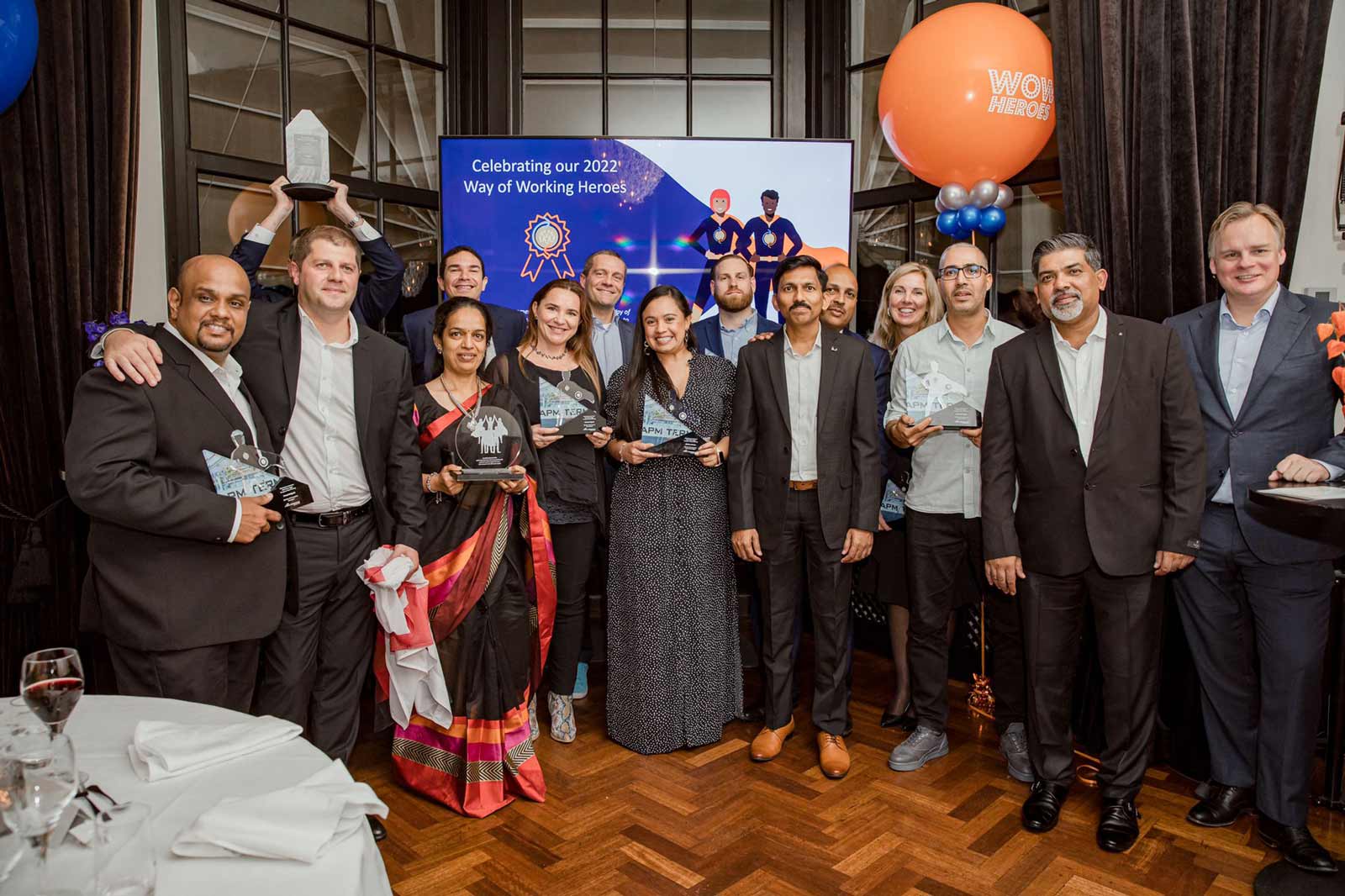
Investment in ‘Lean’ practices improves efficiency for APM Terminals customers
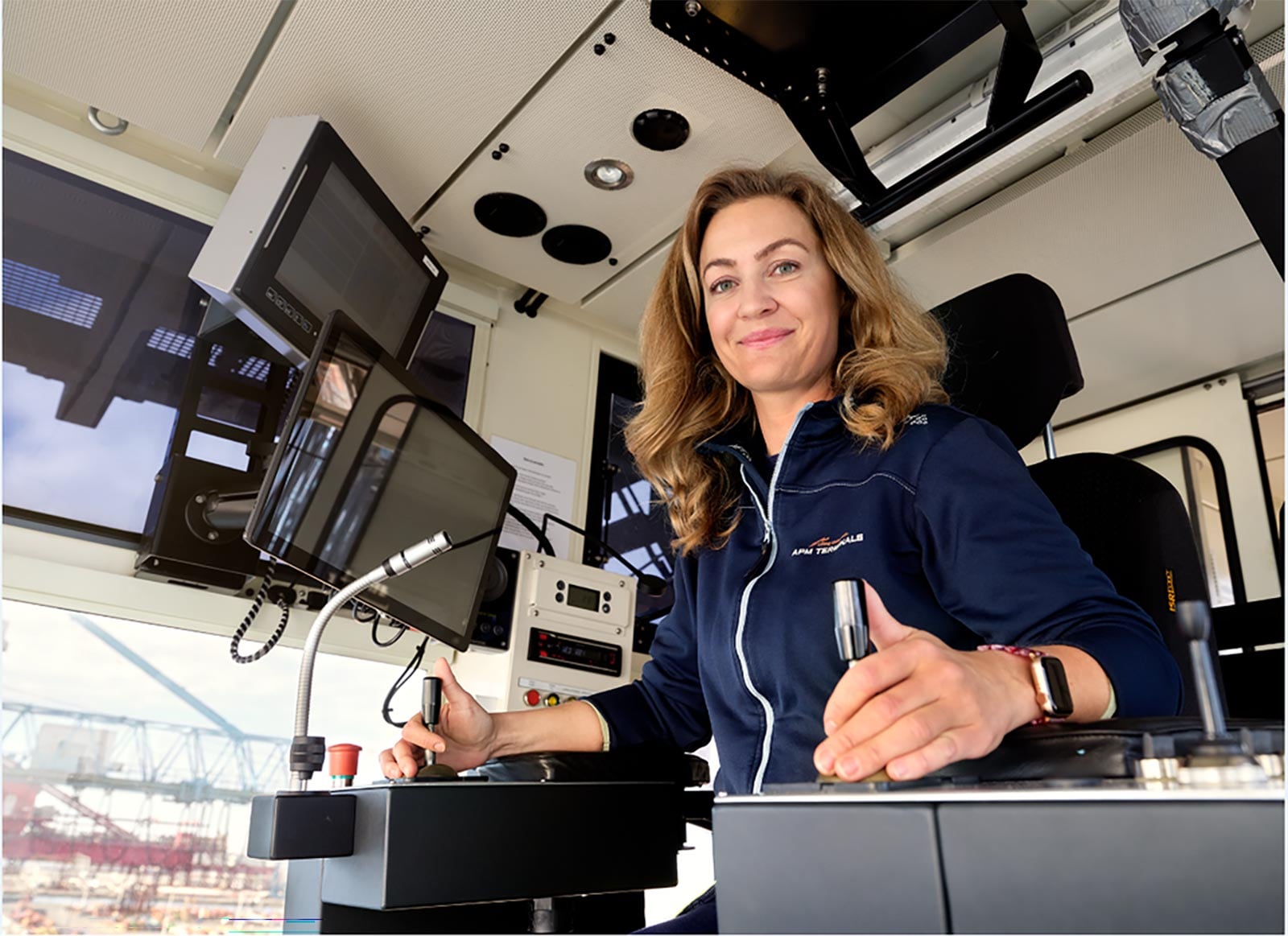